By Eric Gersh, GM - Custom Switchgear
If your facility’s priorities involve safety, extending equipment life, or meeting a budget, mastering switchgear preventative maintenance is essential to achieving your goals. This article will guide you through the five most important things to consider for switchgear PM.
1- Properly Isolate Your Switchgear
Nothing is more important than safety, so knowing how to correctly isolate your equipment is priority number one. Find out if your system has a single source, is double-ended, or if it has tiebreakers. Then, identify potential backfeed issues, either from a generator or someone testing a transformer downstream that is not isolated properly. Make sure you have the proper amount of lockout tagout (LOTO) equipment and never assume your equipment is de-energized; it is crucial that LOTO rules are always followed. Switchgear often has control power coming from other locations and comes
in various voltages (120VAC, 125VDC, 250VDC, etc.).
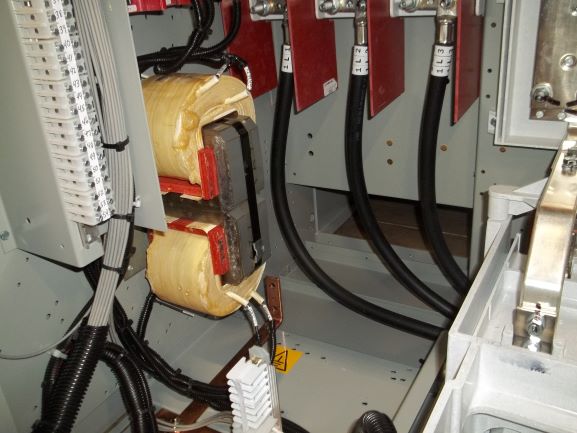
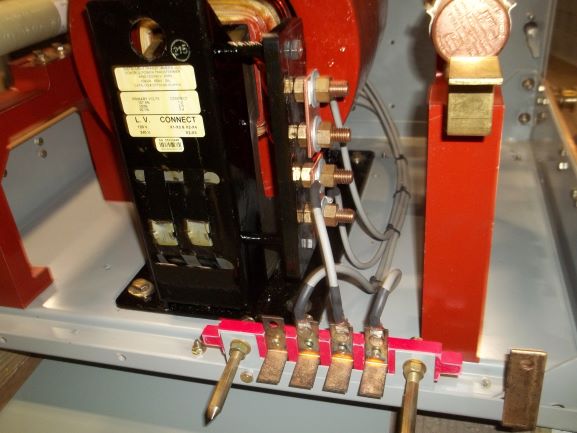
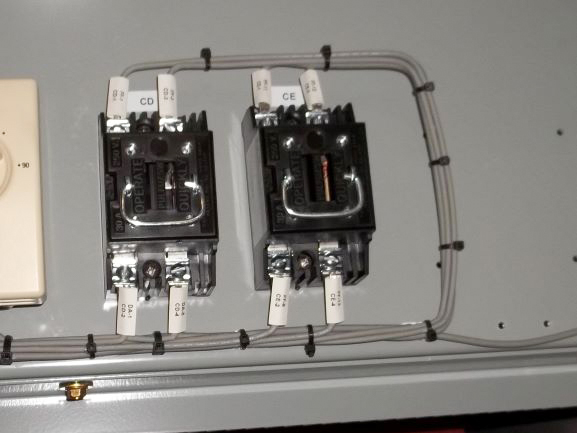
2- Determine Your Equipment’s Environment
Knowing what type of environment your equipment is in can guide many of your PM decisions. If the switchgear is dusty, is it from normal, outdoor dust, smoke, or coal dust? Different types of contaminants may require different types and quantities of cleaning products and supplies, like vacuum filters and rags. For example, if you have porcelain insulators, waxing may be necessary (consult the manufacturer for the type needed). If the insulators are epoxy type, lint-free rags and alcohol may be all that’s needed.
Some environments have higher chemical vapors, which can quickly corrode metal parts (especially electronic equipment). Make sure that you take pictures to document and pay attention to the physical condition of your equipment. If you find that silver-plated parts are corroding or badly discolored, infrared scans may be needed to ensure that no there are no hotspots developing, which can be a catastrophic failure point.
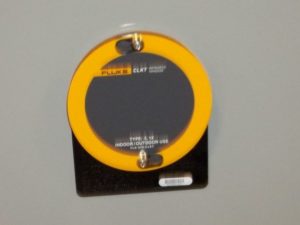
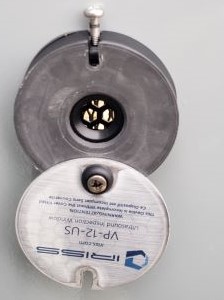
3- Use Procedures Specific To Your Equipment Type
Know what type of equipment you are going to PM. At a minimum, you should have basic procedures that outline what is needed for each type of equipment to be serviced, such as load break switches, air circuit breakers, vacuum circuit breakers, and motor starters. Also, remember to check for bolt tightness and insulation coverings (cables & bus) as well as inspect surge arresters and instrument transformers. The procedures should include which type of lubrication to be used, where and how to apply the lubrication, test voltages for Hi-Pot and Meggers, relay information for testing both electromechanical and digital relays, torque wrench requirements, and TTR testing details. Find out if the equipment you have uses a specific type or brand of lubrication. In some cases, using the incorrect product will void a warranty or is less effective than the materials the manufacturer used.
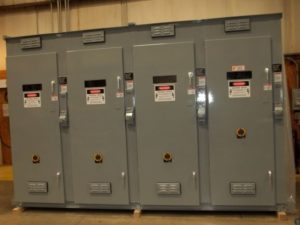
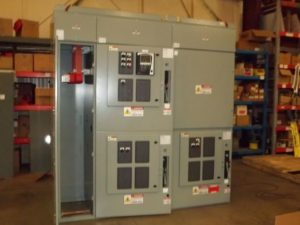
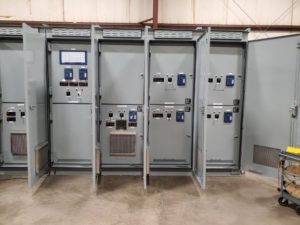
4- Develop a Switchgear Preventative Maintenance Plan
Develop a schedule for how often you plan to PM your switchgear. NETA Appendix B lays out a general program to follow for preventative maintenance. It takes into consideration such things as the criticality of equipment, equipment condition, and type of equipment. These are just guidelines, but they provide a great start to developing an effective PM schedule. If you maintain your equipment on a schedule that minimizes the effects of contamination and wear, reliability and uptime will increase and overall cost of ownership will decrease.
Look at the instruction manuals that came with your equipment to see if certain items have specific replacement schedules based on use or age. For obsolete equipment, this can become a challenge. Parts can be very expensive or unavailable, so see if there are retrofits or upgrades that can be done. Southwest Electric Co. can help with locating hard-to-find parts as well as upgrading or retrofitting your equipment. Ignoring these issues will only cost more money and extend any potential downtime.
5- Keep & Trend Your Test Reports
Lastly, make sure to create comprehensive reports for your switchgear preventative maintenance, and study them closely. This is probably the most overlooked part of an effective PM plan. Most just look at flagged or identified item lists for the “found” problems. But, if you invest in studying the test reports and trending the results, potential problems can be identified long before failure or service interruption takes place. This saves time by determining if the PM frequency can be adjusted to meet the equipment’s real need. Studying reports can also guide you on where to spend (or save) your resources, help you avoid catastrophic equipment failure, and ultimately help keep your personnel from experiencing potentially catastrophic events.
If you are using a third-party testing or a switchgear preventative maintenance company, see if they can format the test reports to make trending easier to follow. Set limits that can be color coded to make identifying negative trends easier to spot.
By following these basic principles, your electrical equipment should be reliable, trouble-free and safe for many years. At Southwest Electric Co., we’re experts at designing and servicing switchgear, and we’re here to help solve all of your equipment needs. We can provide maintenance solutions, studies, upgrades, custom fabrication, and more. Give us a call or an email, and we will be happy to get the conversation started.